If you’re evaluating the build quality of electronic locks for commercial applications, it’s important to consider the materials used. Most high-grade electronic locks are constructed from stainless steel, brass, or hardened steel to ensure resistance against tampering and physical force. For enhanced durability and corrosion resistance, many models also incorporate advanced alloys like zinc or aluminum. Understanding these materials helps dealers and commercial buyers assess product reliability, longevity, and suitability for demanding environments. This overview explains how each material contributes to the overall performance of professional-grade smart locks.
Key Takeaways
- The use of high-grade materials like stainless steel, brass, and hardened steel significantly enhances the security and lifespan of electronic locks, making them ideal for demanding commercial environments.
- Lightweight yet durable alloys such as zinc and aluminum improve lock reliability without compromising strength—perfect for high-frequency access points.
- Advanced surface treatments like powder coating and electroplating add an extra layer of corrosion resistance and aesthetic value, ensuring long-term performance in varied conditions.
Introduction to Electronic Locks
Electronic locks are advanced access control solutions that leverage digital authentication technologies—such as keypads, RFID cards, and biometric sensors—to replace traditional mechanical keys. Designed to reduce the risks associated with lost or duplicated keys, these systems offer a scalable and secure upgrade for commercial, institutional, and industrial facilities.
A key advantage of electronic locks lies in their ability to integrate seamlessly with broader access control systems, enabling features such as remote management, real-time audit trails, and customizable user permissions. This makes them ideal for businesses seeking to strengthen operational security while enhancing user convenience.
Built with reliable electronic components and robust materials, modern smart locks support centralized access control, making them a preferred choice for environments that demand high security, flexible user management, and reduced administrative overhead.
Overview of Materials in Electronic Door Locks
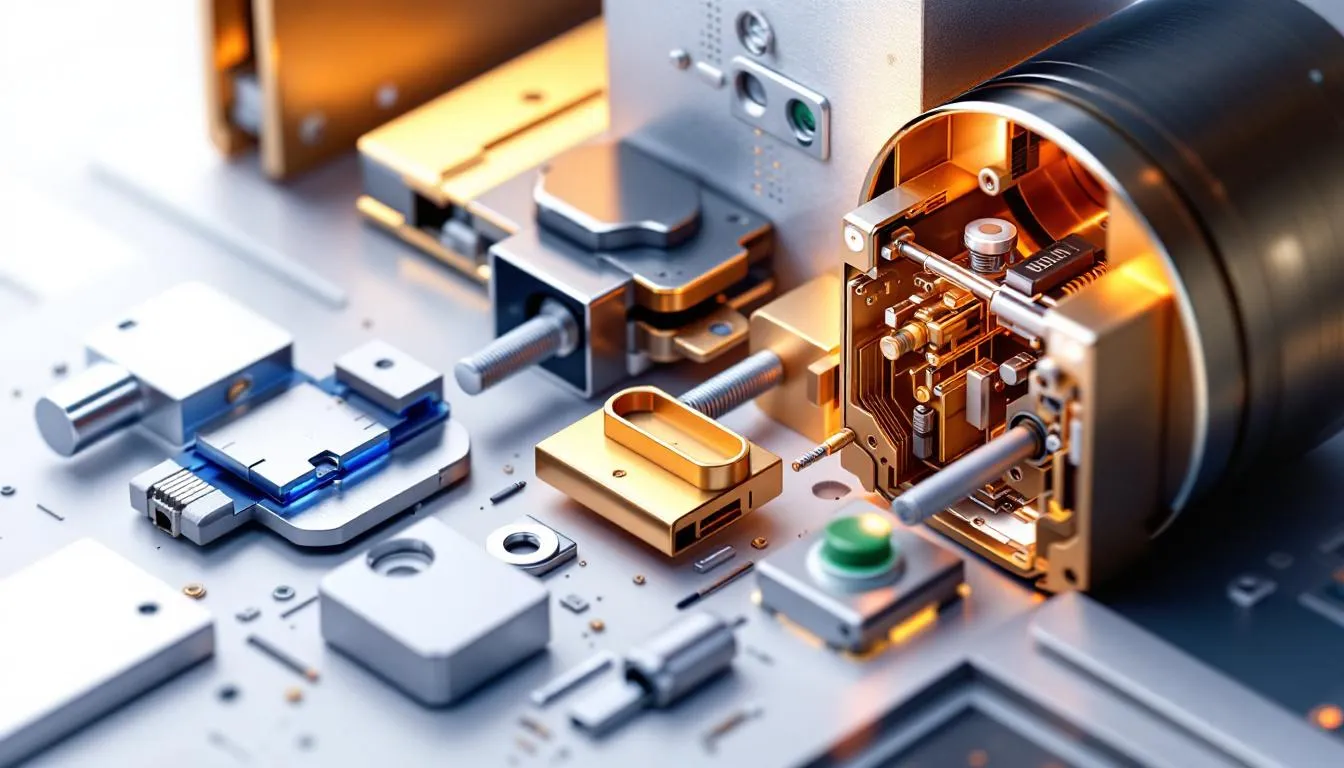
The performance and reliability of electronic door locks are directly influenced by the materials used in their construction. In commercial and residential applications alike, material quality plays a critical role in determining a lock’s durability, resistance to tampering, and long-term operational efficiency. Low-grade materials can compromise both lifespan and security, leading to higher maintenance costs and potential vulnerabilities.
Smart lock manufacturers prioritize premium materials—such as stainless steel, brass, zinc alloys, and hardened steel—to ensure that each unit delivers robust protection and withstands daily wear in demanding environments. Whether for cabinet locks, digital door locks, or enterprise-grade access control systems, material selection is customized to meet the technical and aesthetic demands of each application.
For distributors and commercial buyers, offering electronic locks built with high-quality components means delivering long-term value, reduced failure rates, and better customer satisfaction. In the sections that follow, we explore the core materials used in modern electronic locks and how each contributes to performance, appearance, and security.
Types of Electronic Locks
Electronic locks are available in a wide range of types, each designed to meet distinct security demands across residential, commercial, and institutional environments. For distributors and system integrators, understanding these variations is critical to recommending the right solutions to clients and end users.
Electronic Door Locks
Electronic door locks are engineered for exterior and interior doors, offering advanced keyless access and centralized control. These locks support multiple access methods—such as biometric scans, PIN codes, and mobile credentials—making them ideal for high-traffic buildings or multi-unit properties. For businesses and smart lock dealers, electronic door locks present a scalable solution with features like remote locking, audit trails, and smart home integration. Their flexibility and high security make them a staple in both residential developments and commercial facilities.
Digital Locks
Digital locks, often used on interior doors, lockers, cabinets, and safes, rely on electronic keypads or biometric authentication for access. These locks are particularly valued in office settings and institutional spaces where traditional keys present operational challenges. Digital locks offer minimal maintenance, fast installation, and user-friendly interfaces, making them an efficient upgrade for spaces that require controlled but frequent access.
Electromagnetic Locks
Electromagnetic locks provide high holding force—typically ranging from 600 to 1,200 pounds—and are widely used in commercial and industrial applications. They are ideal for emergency exits, server rooms, and high-security zones where fail-safe configurations and real-time access control are required. Maglocks are compatible with access control systems and offer seamless integration for remote monitoring and centralized security management. For commercial property managers and integrators, electromagnetic locks provide durability, compliance, and robust protection under demanding conditions.
High-Quality Metals for Maximum Security
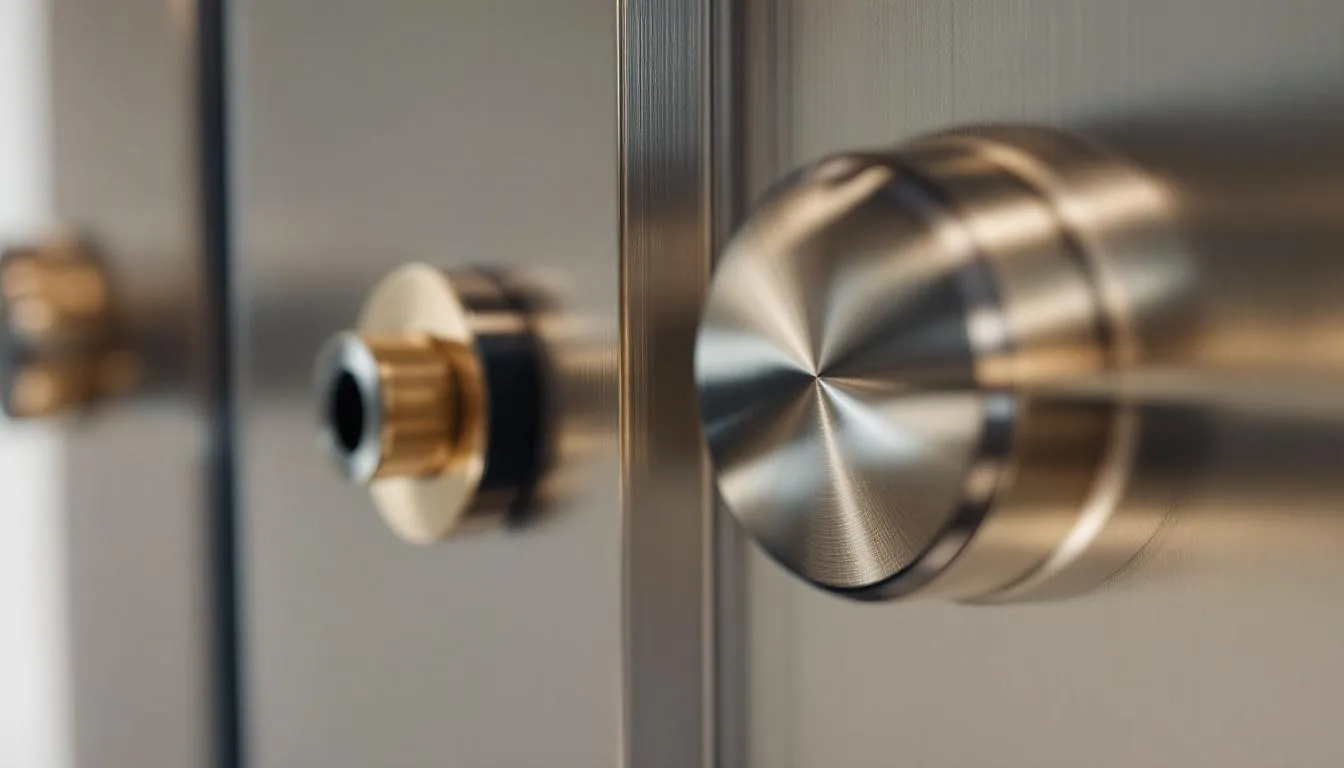
For distributors and commercial buyers, the material composition of an electronic door lock is a key indicator of its performance, security, and longevity. Premium metals such as stainless steel, brass, and hardened steel are widely used in commercial-grade smart locks due to their superior resistance to tampering, corrosion, and physical force. Components like strike plates, latch bolts, and lock bodies benefit directly from the structural strength of these metals, offering end-users long-term reliability across demanding environments.
Stainless Steel
Stainless steel is the preferred choice for outdoor and humid environments thanks to its high corrosion resistance and minimal maintenance needs. Locks built with stainless steel maintain structural integrity over time and are less likely to degrade under moisture, making them ideal for coastal areas, outdoor gates, or commercial facilities exposed to harsh weather.
Brass
Brass is known for its excellent machinability and visual appeal, making it popular for lock cylinders and trim components. Electroplated brass resists rust and discoloration, giving electronic locks a refined appearance without compromising durability. Its balance of strength and aesthetics makes brass a strategic material in projects where both security and design matter—such as upscale residential or hospitality installations.
Hardened Steel
Hardened steel is essential in high-security electronic locks. It is used in areas most vulnerable to physical attacks, such as deadbolts, internal locking mechanisms, and reinforced strike plates. Through a heat treatment process, hardened steel gains exceptional tensile strength, making it highly resistant to prying, sawing, and impact—perfect for commercial properties, banks, and institutional facilities requiring Grade 1 ANSI/BHMA-rated solutions.
For B2B buyers, understanding these material advantages can guide purchasing decisions and strengthen value propositions when selling to end users. High-grade metals aren’t just about strength—they are a core component of delivering reliable, professional-grade access control solutions.
Advanced Alloys for Enhanced Durability
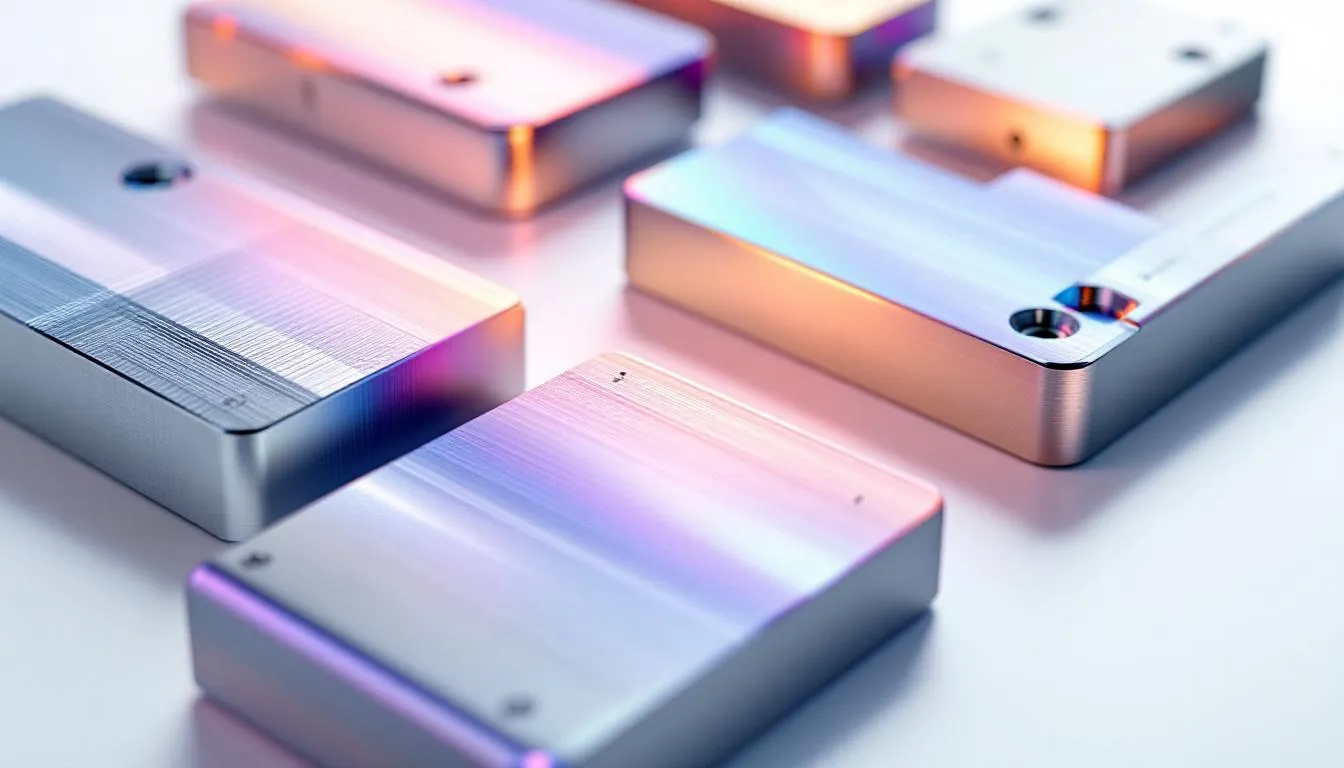
For smart lock manufacturers and B2B buyers, the material composition of a locking system directly influences product performance, installation efficiency, and lifecycle value. Advanced alloys like zinc alloy and aluminum alloy are widely used in electronic locks for their superior strength-to-weight ratio, resistance to tampering, and adaptability across diverse environments.
Zinc Alloy
Zinc alloy is a preferred material in electronic lock housings and internal components due to its excellent castability, dimensional precision, and corrosion resistance. Its lightweight nature allows for ease of installation without sacrificing mechanical strength, making it ideal for volume production in both residential and commercial-grade smart locks. In addition, zinc alloy supports detailed aesthetic finishes—an advantage in premium projects where visual appeal must match security performance.
This material’s robust wear resistance and ability to tolerate environmental stress (e.g., humidity, temperature fluctuations) enhance product longevity, which is critical for applications in hospitality, retail, and high-traffic office environments.
Aluminum Alloy
Aluminum alloy is another high-performance material used in smart lock construction, valued for its lightweight yet rigid structure. This alloy is especially advantageous for electronic locks intended for larger commercial doors, entry gates, or multi-unit housing, where both strength and weight efficiency matter.
Its natural corrosion resistance and thermal stability make it suitable for outdoor applications, while the reduced weight improves logistics and simplifies retrofitting into existing infrastructures. For distributors and commercial installers, aluminum-based lock models offer a strong return on investment due to lower failure rates and reduced maintenance needs.
In summary, integrating zinc and aluminum alloys into electronic lock manufacturing ensures durability, streamlined production, and long-term field reliability—key priorities for B2B clients focused on quality, performance, and operational efficiency.
Electronic Components and Their Materials
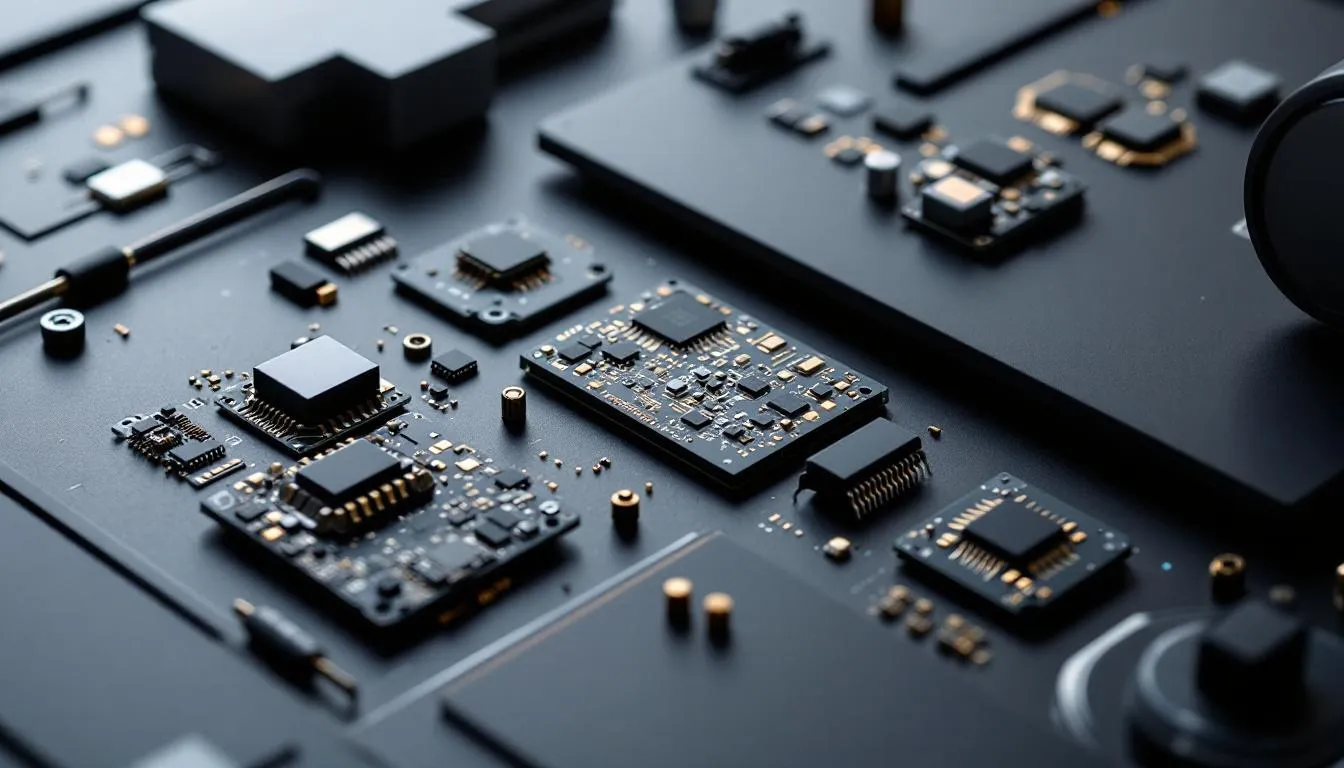
Beyond exterior hardware, the internal electronic components of a smart lock are critical to its long-term reliability and performance—especially in commercial deployments. Core components such as circuit boards and actuators or micro motors must be engineered with precision and constructed from high-quality materials to ensure consistent operation under various conditions.
Circuit Boards
Serving as the lock’s command center, the PCB (printed circuit board) processes authentication requests, user credentials, and system signals. For enterprise-grade smart locks, circuit boards must be manufactured using heat-resistant substrates and moisture-tolerant coatings, ensuring durability in fluctuating environments such as building exteriors or high-traffic entrances.
Whether the lock supports multi-factor authentication, RFID, or mobile credentials, the reliability of the circuit board is paramount. A well-designed board ensures fast processing and accurate response to biometric scans or keypad inputs—minimizing access delays and system failures. In cloud-connected models, the board also facilitates secure data transmission and real-time remote access via internet-based platforms.
Actuators and Motors
Micro actuators and DC motors are responsible for the mechanical movement of the locking mechanism. These components must be both responsive and durable to meet commercial standards. In B2B applications—such as hotels, office buildings, and industrial access points—actuator performance is measured in lifespan cycles, often exceeding 200,000 lock/unlock operations without failure.
Premium smart lock manufacturers utilize zinc or aluminum alloy motor casings for heat dissipation and corrosion resistance. These materials extend motor life, reduce friction, and ensure smooth engagement of the bolt or latch, even during extended use or power fluctuations.
Reliable internal engineering is especially vital for locks operating in battery-dependent systems. Backup features such as external charging ports or 9V battery emergency access help mitigate power failure risks, ensuring uninterrupted security.
Protective Coatings and Finishes
For commercial-grade electronic locks, protective coatings and surface treatments play a critical role in enhancing product durability, resistance to environmental wear, and visual appeal. These finishes not only preserve the lock’s functionality over time but also ensure it aligns with modern design standards—making them suitable for residential, hospitality, and commercial installations.
High-quality finishes serve two primary purposes: they shield internal components from moisture, dust, and corrosion, and they deliver a polished, professional appearance that aligns with various architectural aesthetics.
Powder Coating
Powder coating is a widely adopted surface finishing method in electronic lock manufacturing. It involves applying a dry powder to metal surfaces, which is then heat-cured into a hard, uniform layer. This coating provides excellent resistance to chipping, scratching, UV exposure, and fading—making it ideal for locks installed on high-traffic doors or outdoor gates.
Beyond performance, powder coating offers flexibility in color customization and surface texture, allowing distributors and OEMs to tailor product lines for residential, hotel, or office use. This not only enhances branding opportunities but also increases the lock’s market appeal across different buyer segments.
Electroplating
Electroplating adds a layer of metal—such as nickel, chrome, or zinc—onto the lock’s exterior to increase corrosion resistance, surface hardness, and wear durability. This is especially important for outdoor electronic locks or those in coastal or industrial environments where humidity and chemical exposure can degrade lesser finishes.
From a supplier’s perspective, electroplated finishes offer a long-lasting, high-gloss or satin aesthetic, while also reducing maintenance requirements for end users. For B2B customers managing large-scale deployments, electroplated locks represent a lower total cost of ownership through improved resilience and extended product lifespan.
Environmental Considerations in Material Selection
For electronic lock suppliers and commercial integrators, selecting the right materials goes beyond aesthetics—it’s essential for long-term reliability and performance in demanding environments. Locks deployed in outdoor settings, industrial facilities, or moisture-prone areas must withstand chemical exposure, extreme weather, and fluctuating temperatures without compromising functionality or appearance.
Lightweight yet durable materials such as zinc alloy, aluminum, and stainless steel are preferred for their strength-to-weight ratio, which simplifies professional installation while delivering robust protection. These materials are widely used across digital door locks, maglocks, and cabinet locking systems, ensuring both security and operational efficiency in commercial settings like hotels, offices, and institutional facilities.
To further extend product lifespan, protective surface treatments—such as powder coating and electroplating—are applied to resist environmental wear and enhance corrosion resistance. This is especially critical for emergency exit doors, outdoor electronic locks, and access-controlled cabinets where continuous operation is vital.
Corrosion Resistance
Corrosion resistance is a non-negotiable feature for smart lock materials, especially in coastal, humid, or chemically exposed environments. Premium materials like stainless steel and treated zinc alloys maintain their structural integrity and appearance over time, reducing maintenance and replacement costs for property managers and distributors.
Temperature Tolerance
Electronic locks must perform reliably across a wide temperature range (-20°C to 70°C). Whether used in unheated warehouses or high-temperature zones, smart locks made with thermally stable materials ensure uninterrupted operation—even under fire-rated compliance or rapid climate shifts. This performance is essential for maintaining secure access in critical environments without compromise.
Importance of Using Top Quality Materials
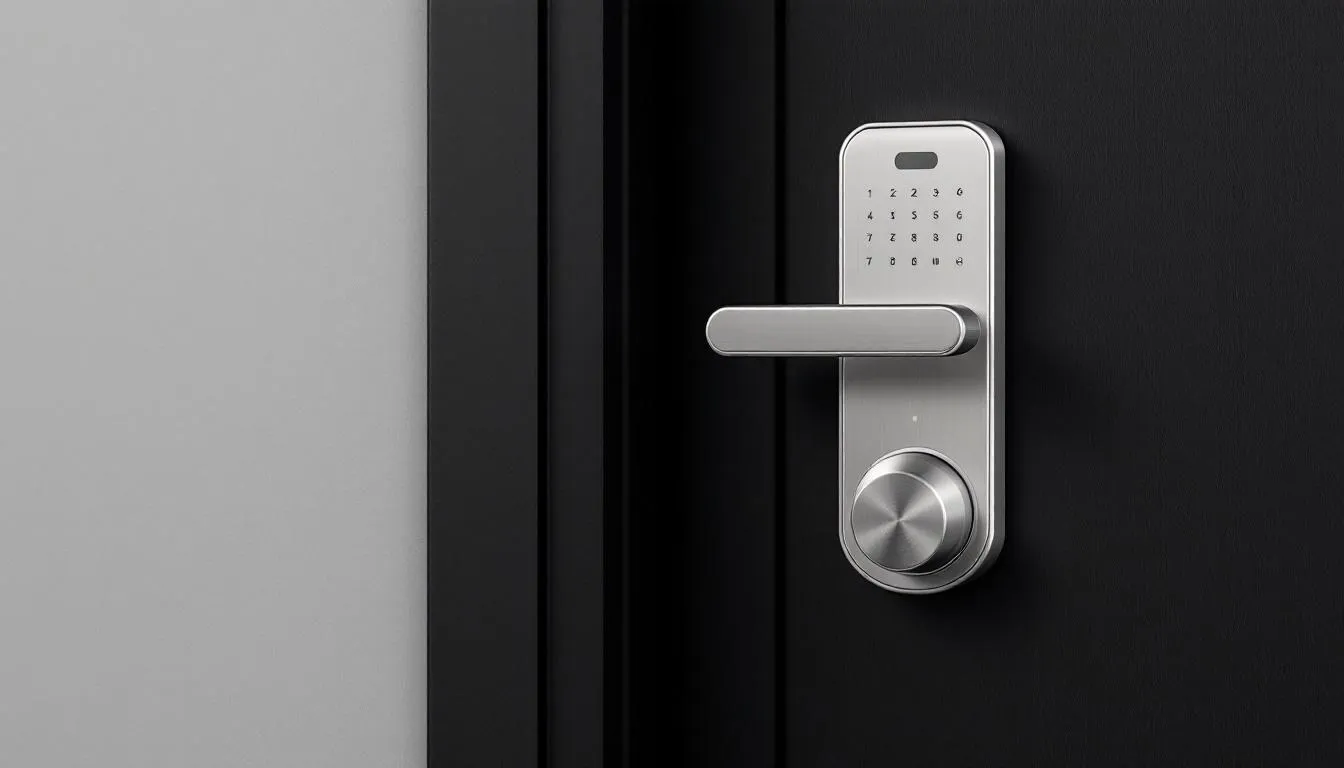
For commercial buyers and system integrators, material quality is a key differentiator in electronic lock performance and longevity. High-grade electronic locks are engineered using premium materials such as zinc and aluminum alloys, which offer excellent durability, tamper resistance, and long-term reliability—essential for high-traffic or demanding environments.
To further enhance product resilience, protective finishes like powder coating are applied to deliver a tougher, chip-resistant surface compared to traditional paint. These coatings not only preserve the lock’s mechanical integrity but also maintain its aesthetic appeal, even after prolonged use or exposure to environmental stress. For projects where both performance and presentation matter—such as hotels, offices, and multi-unit developments—investing in high-quality, coated electronic locks ensures greater customer satisfaction and reduced maintenance costs.
Conclusion: Why Material Selection Matters in Electronic Locks
From a supplier’s standpoint, the materials used in electronic door locks directly impact their security performance, service life, and commercial value. Stainless steel, brass, and hardened steel deliver exceptional resistance to tampering and forced entry, while zinc and aluminum alloys offer a lightweight yet durable solution ideal for large-scale deployments.
For distributors and commercial clients, understanding these material differences enables better product recommendations and procurement decisions. Choosing locks built with premium materials ensures superior reliability, lower maintenance costs, and long-term customer satisfaction—key advantages in today’s competitive access control market.
Frequently Asked Questions
Why is stainless steel a popular material for electronic locks?
Stainless steel is widely used in electronic locks due to its exceptional corrosion resistance, mechanical strength, and long-term durability. These properties make it ideal for both indoor and outdoor applications where environmental exposure is a concern. For commercial buyers and system integrators, stainless steel ensures that smart lock systems maintain performance and appearance over time, even in high-traffic or harsh settings. Its resistance to rust and wear supports low maintenance costs and increases product reliability—key factors in large-scale deployments and professional installations.
What makes brass a good choice for electronic lock components?
Brass is commonly used in electronic lock components thanks to its high mechanical strength, corrosion resistance, and premium finish. Its natural durability makes it suitable for high-frequency use in commercial environments, while its malleability allows for precise machining of internal components such as key cylinders and latches. Electroplating further enhances brass’s resistance to oxidation and wear, making it both aesthetically refined and structurally reliable—ideal for clients who value both security performance and visual appeal. The only problem is that it’s very expensive.
How do advanced alloys like zinc and aluminum contribute to the durability of electronic locks?
Advanced alloys such as zinc and aluminum play a critical role in improving the durability and performance of electronic locks. These materials offer an ideal combination of lightweight design, high tensile strength, and corrosion resistance, making them especially well-suited for commercial and high-use environments. Their resilience against wear and environmental stress helps ensure long-term reliability and reduced maintenance, making them a preferred choice for manufacturers and buyers seeking dependable, high-quality locking solutions.
What role do protective coatings play in electronic locks?
Protective coatings are essential for extending the lifespan and maintaining the performance of electronic locks. In commercial and high-traffic environments, these coatings—such as powder coating and electroplating—offer critical protection against corrosion, UV exposure, scratches, and general wear. They not only preserve the lock’s structural integrity but also ensure a consistent, professional appearance over time. For dealers and commercial buyers, locks with durable protective finishes deliver lower maintenance costs and improved aesthetic value, making them a smarter long-term investment.
Why is it important to consider environmental factors when selecting materials for electronic locks?
For B2B buyers and commercial installers, selecting electronic locks built with materials that withstand harsh environmental conditions is critical. Humidity, salt air, and temperature extremes can degrade lock performance over time. Choosing materials with high corrosion resistance—such as stainless steel or zinc alloys—and proven temperature tolerance ensures long-term reliability and security. These properties are especially vital for outdoor installations or facilities in challenging climates, where maintaining operational stability and reducing maintenance costs are key business priorities.